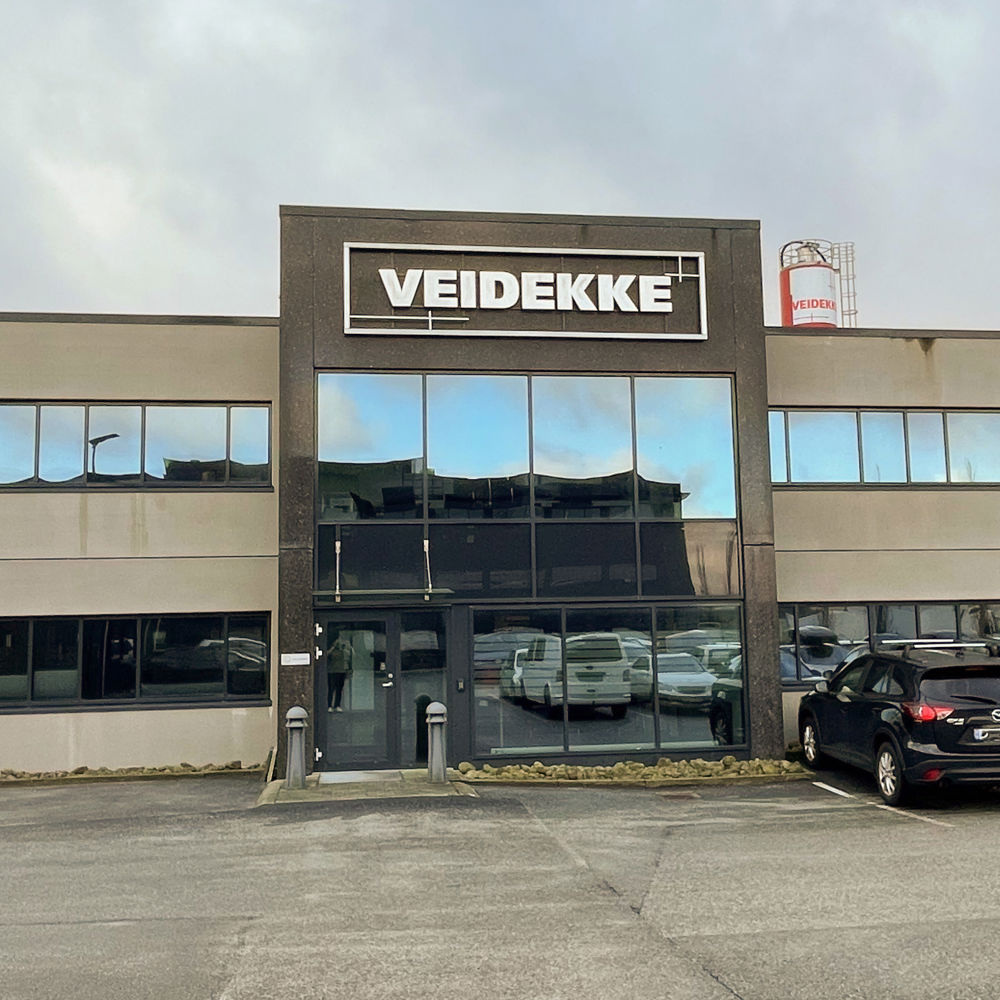
Navneskifte og fremtidsvyer
Ved nyttår skiftet Block Berge Bygg navn til Veidekke Prefab. Med nytt navn og gammel storhet er betongelementfabrikken på Klepp klar for fremtida.
Elementprodusenten Veidekke Prefab på Jæren ligger så langt fremme på bærekraft og teknologi at de kunne vunnet priser, men de har aldri ropt høyt om det de gjør. Med økt kapasitet og nytt navn er de klare for å heve stemmen.
Daglig leder i Veidekke Prefab, Aage Tengs.
- Da jeg kom hit for to år siden, på utleie fra Veidekke, slo det meg at gjengen her er så beskjedne at de ikke skjønner selv hvor flinke de er, sier daglig leder Aage Tengs. - De søker ikke oppmerksomhet for sine gode løsninger, de bare finner dem.
Uten de store omveltningene, men ved å bygge stein på stein, har de gjort tiltak som har ført til at de har blitt blant de beste i klassen. Det er som de lange steingjerdene vi har kjørt forbi på veien fra Stavanger til Klepp. Bøndene som lempet på de steinene la neppe merke til når gjerdene ble storslagne og spesielle. Målet var aldri å imponere, men å få løst problemet med stein i åkerlandet. Men resultatet er enormt.
- Jeg tror det er litt sånn jærsk ånd. Å fikse ting, få det til. Det viktigste er løse oppgaven, ikke fortelle om det. Vi ser utfordringer, og tenker at dette må vi prøve å få til, sier avdelingsleder Geir Hauge Eide. Arbeidsplassen hans har nylig skiftet navn fra Block Berge Bygg til Veidekke Prefab. Men ånden er den samme.
Jeg tror det er litt sånn jærsk ånd. Å fikse ting, få det til. Det viktigste er å løse oppgaven, ikke fortelle om det.
På fabrikken på Klepp produserer om lag 120 fagarbeidere betongelementer til etasjeskillere, veggelementer, søyler, trappesjakter, bjelker, trapper, balkonger og svalganger. Noen kunder bestiller akkurat de elementene de vet at de trenger, andre trekker inn Veidekke Prefab i prosjekteringen slik at de sammen kan finne ut hva som blir den beste løsningen. I de enorme lokalene på 23 000 kvadratmeter er det mulig å lage det meste som kan støpes i betong.
- Det er som en byggeplass, bare at den er under tak og satt veldig i system, sier Geir og viser oss rundt i ryddige og velorganiserte lokaler. Mens betongresepten for et prosjekt doseres automatisk i blandemaskina før massen kjøres i takhengte vogner til rett hall, jobber fagarbeidere med å klargjøre armeringen slik at den kan senkes ned i støpeformene i mest mulig ferdige enheter. Trillebåra med rør og annet som skal støpes inn, står allerede klar. Hvis betongelementet skal ha innstøpt isolasjon, noe prefabrikerte veggelementer ofte har, ligger isolasjonen ferdig kuttet med arbeidstegning for hvordan puslespillet skal legges i støpeforma. Alt dette bidrar til at det kan gå effektivt for seg når støpinga først starter.
Gjøres klar for betongen.
Hvis man blir sittende å vente på den perfekte løsningen, er det fort gjort å ikke få gjort noe. Så vi har bestemt oss for å igangsette også forbedringer som gir små gevinster, og har erfart at gevinsten ofte vokser når vi først setter i gang
Det store kuttet i utslipp gjør de altså ved å bruke minst mulig sement i konstruksjonene og betongresepter med best mulig klimaavtrykk. Men samtidig er de opptatt av at alle kutt teller.
- Hvis man blir sittende å vente på den perfekte løsningen, er det fort gjort å ikke få gjort noe. Så vi har bestemt oss for å igangsette også forbedringer som gir små gevinster, og har erfart at gevinsten ofte vokser når vi først setter i gang, sier Aage Tengs.
- Her kommer innspill og gode ideer fra alle ledd i systemet, fra ledere til servicepersonell og fagarbeidere. Alle bruker sin erfaring og praktiske innsikt til å se store og små muligheter til forbedringer, og det har virkelig vært kjekt å se fagarbeidernes engasjementet for vår økte satsning på klimavennlige løsninger, sier Geir Hauge Eide.
Testing av forskjellige betongkvaliteter.
Egil Lode, Aage Tengs og Heine Knudsen inne ved blandemaskinene.
Veidekke Prefab bruker mye vann i produksjon og renhold, og har tradisjonelt fått dette via kommunale vannledninger. En dag dukket tanken opp: Vi har 23 000 kvadratmeter flatt tak som samler opp regnvann. Hvorfor kan vi ikke bruke dette i produksjonen?
- Når noen kommer med et forslag som virker godt, tester vi det ut, så fremt det verste som kan skje er at vi må gå tilbake til den gamle løsningen hvis det ikke funker. Det har gitt oss flere nyskapninger for redusert svinn og økt effektivitet i produksjonen, sier han.
- Faktisk førte en omlegging av måten vi utnytter de bevegelige støpebordene våre på, til at vi i fjor utvidet kapasiteten med 35 prosent, forteller Aage Tengs, som mener at miljøet på Klepp slår hull på myten om at ungdom og innovasjonsevne henger sammen.
- Vi har høy gjennomsnittsalder på våre ansatte, for de trives så godt at ingen slutter. Men det at de er erfarne, stolte og lojale står ikke i noe motsetningsforhold til å være på jakt etter forbedringer.
Når noen kommer med et forslag som virker godt, tester vi det ut, så fremt det verste som kan skje er at vi må gå tilbake til den gamle løsningen hvis det ikke funker. Det har gitt oss flere nyskapninger for redusert svinn og økt effektivitet i produksjonen
Testing av betongkvaliteter.
- Vi spesiallager alt, for det er ikke sånn at one size fits all. Men vi gjør det på en standardisert måte som er svært tidsbesparende, sier Geir Hauge Eide. Hadde de gått for standardløsninger, måtte alt vært overdimensjonert - for sikkerhets skyld. Og er det noe Veidekke Prefab ikke vil, så er det å bruke unødig mye betong.
- Denne fabrikken har for alvor tatt inn over seg at bransjen vår på mange måter er en klimaversting, sier han.
Produksjon av sement, som det finnes mye av i betong, skaper store CO2-utslipp, det kommer man ikke utenom. To tredjedeler av klimagassutslippene i sementproduksjon kommer nemlig fra selve den kjemiske prosessen, og vil ikke kunne fjernes selv om man for eksempel bruker utslippsfri energi. Sementproduksjon står for om lag sju prosent av alle menneskeskapte klimagassutslipp. Den virkeligheten forholder gjengen på Veidekke Prefab seg til. De snakker om "det grå skiftet" og ønsker å endre holdningene til betongbransjen.
- Om vi tilhører en verstingbransje, skal vi i hvert fall være best av verstingene, og pushe utviklingen rett retning. For å redusere utslippene så det forslår, må vi redusere sementmengden og velge sementtyper med minst mulig utslipp, for i klimaregnskapet til Veidekke Prefab er sementen det store, store kakestykket, sier Geir Hauge Eide.
Vi dekker den ekstra utgiften, rett og slett fordi det er det rette å gjøre
"Fargegata" ved inngangen til fabrikken er inspirert fra gatene i Stavanger.
Likevel er det noen avgjørelser som må tas av noen med beslutningsmyndighet, som da Veidekke Prefab bestemte seg for å stille krav om at alle som kjører for dem skal bruke biodiesel.
- Vi dekker den ekstra utgiften, rett og slett fordi det er det rette å gjøre.
Og sist, men ikke minst, er det selvsagt prosjekter som krever større forberedelser og utviklingsarbeid. Utvikling av betongelementer med integrerte solceller er et eksempel på det siste. Demonterbare bygningselementer og en mulig panteløsning der gamle bygg blir knust og tatt inn i produksjonen igjen, er også på trappene. Utviklinga fortsetter på Veidekke Prefab.
Ved nyttår skiftet Block Berge Bygg navn til Veidekke Prefab. Med nytt navn og gammel storhet er betongelementfabrikken på Klepp klar for fremtida.
Her kan du lese siste nytt fra og om oss i Veidekke.
Veidekke Prefab er en av Norges ledende aktører innen prefabrikkerte betongelementer. Vi prosjekterer, produserer, transporterer og monterer råbygg til private og offentlige kunder i hele Skandinavia.
Avdelingsleder Prosjektutvikling Veidekke Prefab
HMS-leder og fagarbeideransvarlig Veidekke Prefab