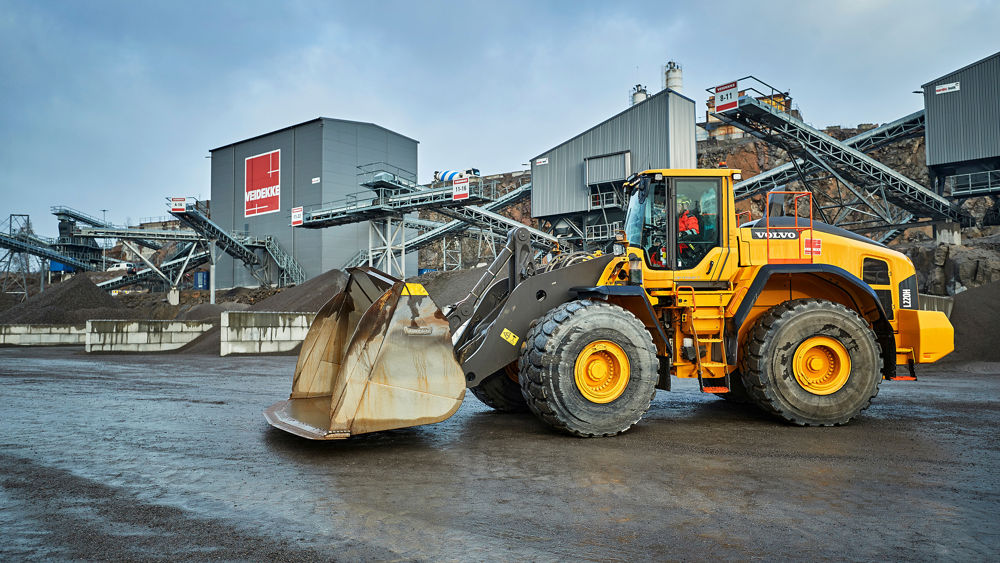
Enheter og datterselskaper
Vi består av en rekke enheter, avdelinger og selskaper. Her finner du kontaktinformasjon til våre enheter og datterselskaper i Norge.
Det begynte med brostein i Norge i 1936. I dag bygger Veidekke veier, tunneler, broer og bygg i hele Skandinavia. Vi setter mennesker først.
Vi består av en rekke enheter, avdelinger og selskaper. Her finner du kontaktinformasjon til våre enheter og datterselskaper i Norge.
Vi er mange du kan spørre hvis det er noe du lurer på.
Når vi setter oss nye mål, er det alltid med menneskene først. Les mer om vår strategi frem mot 2025.